提示:本文通过对调节阀的原理、流量特性、结构类型的阐述,介绍了三通调节阀在蓝星0kt/a有机硅单体工程项目中的应用。
1 控制阀的节流原理
从流体力学的观点看,控制阀是一个局部阻力可以变化的节流元件,对不可压缩流体,由伯努利方程可以求得通过控制阀的流体流量,如式(1):
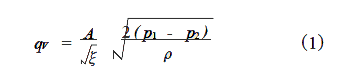
式中 qV———体积流量;
p1———阀前压力;
p2———阀后压力;
A———节流面积;
ξ———控制阀的阻力系数;
ρ———流体的密度。
由式(1)可见,当A一定,p1–p2不变时,qV仅随控制阀阻力系数的变化而变化:若ξ减小,则qV增大;反之,若ξ增大,则qV减小。控制阀就是根据控制信号的大小和方向改变阀芯的行程来改变阀的阻力系数,以达到调节流体流量的目的。
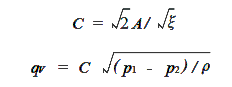
式中C———控制阀的流通能力。
C的定义:温度为5~40℃的水,当控制阀全开,阀两端的压差为0.1MPa,每小时流经控制阀的流量数(m3/h)。控制阀流量系数将由C系列变为KV系列。C和KV之间的关系为:KV=1.01C。
2 控制阀的流量特性
指介质流过控制阀的相对流量与控制阀的相对开度之间的关系,如式(2)所列。
qV/qVmax=f(l/lmax)(2)
式中qV/qVmax———相对流量,即控制阀某一开度下的流量与全开流量之比;
l/lmax———相对开度,即控制阀某一开度下的行程与全开时行程之比。
一般来说,改变控制阀的阀芯与阀座之间的节流面积便可调节流量,但实际上由于各种因素的影响,在节流面积变化的同时,还会发生阀门前后压差的变化,而压差的变化也会引起流量的变化。因此,流量特性有理想流量特性和工作流量特性。
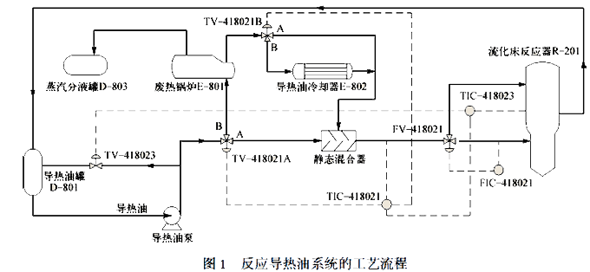
该反应系统是在铜催化剂作用下,以硅粉和氯甲烷为生产原料,在流化床反应器中直接合成粗甲基氯硅烷混合含尘气体,利用一级旋风除尘器除尘后,合成气进入后续系统中净化分离,最终生成甲基单体。
每周期开车前,先用导热油对流化床反应器硅粉床层升温,来自反应器粉料气流输送机的干燥粉料,以及来自氯甲烷气体过热器的过热氯甲烷气体,被导热油预热到合成反应开始的温度,在铜催化剂催化条件下,使氯甲烷与硅粉进行合成放热反应。放热产生的热量被导热油带出,用于产生中压饱和水蒸汽。
反应器的导热油加热结构分两部分,反应器外部为半管夹套,保证外部热量分布均匀;反应器内部为指型管加热,指型管均匀分布使传热均匀,反应器开车升温及正常反应冷却采用导热油提供和带走热量,回收反应热用以副产中压蒸汽。
开车阶段,流化床反应器(R-201)需进行升温时,先向反应导热油罐(D-801)注入一定量的导热油,开启反应导热油泵,将导热油送进流化床反应器内部的指型循环管和外部的半管夹套,进行流化床反应器的床层升温。返回D-801降温后的导热油,再次进行循环加热。当流化床反应器的床层温度达到指定值时,通入过热氯甲烷开始正常生产。正常生产时,用导热油吸收合成反应放出的热量。导热油进反应器时的温度为250℃,出反应器时的温度升到260℃。导热油出反应器后直接进入反应导热油罐,与反应导热油泵旁路返回的导热油混合。
反应导热油泵把加热后的导热油经三通阀(TV-418021A),一部分送到废热锅炉(E-801);另一部分进入流化床反应器(R-201)。两部分的流量是由三通调节阀的阀芯同步反向调节三通阀的A、B出口的开度来分配,这种流量调节方式无节流,流阻小,作用在阀上的压力相对较小,不会对泵产生背压,使导热油泵的导热油流量保持恒定。若流化床反应器的温度发生变化,温度信号经控制系统进行运算,控制三通阀的执行机构带动该阀的阀芯动作,从而改变了三通阀的A、B口的开度,达到调节流量的目的。假设R-201温度偏高,TIC-418023调节器将起作用:一是加大进入到R-201中的导热油流量,以移走R-201中更多的热量,使温度降下来。同时,TIC-418023还要改变调节器TIC-2418021的设定值,使其输出变化,从而改变三通阀 TV-418021A/B阀门的开度———首先加大进入E-801的流量,利用E-801降低进入的导热油的温度,从而降低R-201的温度,在E- 801中,利用被加热的导热油的热量,生产1.0MPa(G)的饱和蒸汽,换热后的导热油直接进入反应器;如果出E-801的导热油温度偏高,即此时R- 201的温度还继续偏高,则利用导热油冷却器(E2802)处的三通阀(TV-418021B),将导热油转向旁路去导热油冷却器,E-802用循环冷却水冷却,即改变三通阀TV-418021B的B出口,进入E-802的油量加大,E-802冷却后的导热油与经TV-418021A的主流导热油在静态混合器中充分混合后去流化床反应器,便更多地降低导热油的温度,最终能用导热油移走R-201中更多热量,使R-201的温度回到设定值上。由三通控制阀(FV-418021)定量控制的导热油进流化床反应器半管夹套管,余下的导热油去流化床反应器内部指型循环管束。
在有机硅单体的生产过程中,反应部分是非常关键的,反应器控制得好与坏将直接影响到最终产品———甲基单体的产量和质量。由于甲基单体合成的反应为放热反应,合成反应的操作温度需控制在300℃左右,因此及时把多余的热量移走,才能保证反应的顺利进行。鉴于该反应控制的重要性和关键性,对反应器的控制采用了反应灵敏、调节速度快且控制性能稳定,同时又不是非常复杂的串级调节系统。以反应器温度(TT-418023)作为主调参数,反应器入口的导热油温度(TT-418021)作为副调参数,2台三通控制阀(TV-418021A/B)作为副环的被调对象,当导热油流量、温度发生变化,TT-418021 引起波动,副调节器TIC-418021)立即进行调节,通过TV-418021A/B的开度变化,改变至废热锅炉及导热油冷却器的导热油量来达到不影响到反应器温度的目的。如果导热油流量、温度变化很大,影响到反应器入口温度(TT-418021)及反应器温度(TT-2418023)的变化,这时主调节(TIC-418023)的输出开始发生变化,对副调节器(TIC-418021)来说,它将接受给定值与测量值两方面的变化,从而加速了调节过程,但此调节过程依然通过改变TV-418021A/B的开度实现。除了上述通过串级控制回路来控制流化床反应器的温度外,还由反应导热油泵的回流流量来调节,加快了调节进程。
综上所述,在反应导热油控制系统中采用了3台三通控制阀,可以省掉3台二通阀和3台三通接管,既能简单、有效地进行控制,根据反应器所需的热量进行流量分配,同时又能保证半管夹套及指型管内的流量稳定,使整个系统运行平稳,完全满足工艺要求。
上海减压阀厂-天沃感谢您浏览!