1.引言
阀门是工业领域一种重要的流体控制设备和承压元件,压力试验是工业阀门最重要的性能测试手段。目前,国内、外的阀门压力试验台几乎都为机械一液压式,劳动强度大,工作效率、测试精度均较低。并且,普遍存在着压力试验没有按标准要求与材料特性严密挂钩的现象。加压和保压过程也是粗糙的目测和繁重的手工操作,试验压力和保压时间不能得到有效的保证,由此带来了测试结果的不准确和测试过程的不科学。并且,随着产品参数的提高,测试数据的误差会达到惊人的程度。现代数字控制技术的发展和工业化应用,为改进传统的阀门压力试验过程提供了一种比较现实的方法和途径。
2.压力试验概述
工业阀门的压力试验通常包括:壳体试验、密封试验和上密封试验,试验介质一般为水和空气,试验过程中要保证系统压力达到或超过规定的试验压力后,在规定的保压时间内,检验受试阀门是否达到相应标准规定的性能要求。
2.1 标准与规范
目前,我国阀门行业比较通行的阀门试验标准主要有:GB/T 13927—1992《通用阀门——压力试验》;JB/T9092—1999《阀门的检验与试验》;APl598:2004《阀门的检查和试验》;BS EN 12266:2003《工业阀门——阀门试验》;ISO 5208:1993《工业阀门一阀门的压力试验》等。由于各国在管道规范、压力分等、材料应用等方面的不同,以上标准间有一定的差异,但在试验方法和试验项目上有很大的共性,实际上,各国在标准制定过程中都存在着相互的借鉴。对于试验过程来说,主要的差别在于压力分等和具体阀种的试验项目、试验条件的规定不同。
此外,阀门的试验规范还远不止于以上所列,其他一些工业国家的阀门试验标准也有不同程度的应用,对于一些特殊结构,特殊用途的工业阀门,制造商或用户有时会另外制定检测、试验规范并要求执行。试验设备或装置应尽可能满足相关要求。
2.2 试验过程
2.2.1 壳体试验
阀门的壳体试验是对阀体和阀盖等联结而成的整个阀门外壳进行的压力试验。其目的是检验阀体和阀盖的致密性及包括阀体与阀盖联结处在内的整个壳体的耐压能力。
每台阀门出厂前均应进行壳体试验。在试验过程中不得对阀门施加影响试验结果的外力。试验压力在保压和检测期间应维持不变。用液体做试验时,应尽量排除阀门体腔内的气体。在达到保压时间后,壳体(包括填料函及阀体与阀盖联结处)不得发生渗漏或引起结构损伤。
壳体试验的方法和步骤:封闭阀门进口和出口,压紧填料压盖,使启闭件处于部分开启位置;给体腔充满试验介质,并逐渐加压到试验压力(止回阀类应从进口端加压);达到规定时间后,检查壳体(包括填料函及阀体与阀盖联结处)是否有渗漏。
2.2.2上密封试验
上密封试验是检验阀杆与阀盖密封副密封性能的试验。具有上密封性能要求的阀门都必须进行上密封试验。
上密封试验的方法和步骤:封闭阀门进口和出口,放松填料压盖,阀门处于全开状态,使上密封关闭,给体腔充满试验介质,并逐渐加压到规定的试验压力,然后检查上密封性能。此项试验可在壳体试验之前进行。
2.2.3 密封试验
密封试验是检验启闭件和阀体密封副密封性能的试验。
密封试验之前,应除去密封面上的油渍,但允许涂一薄层粘度不大于煤油的防护剂;靠油脂密封的阀门,允许涂敷按设计规定选用的油脂。
试验过程中不应使阀门受到可能影响试验结果的外力。应以设计给定的方式关闭阀门。密封试验应在壳体试验后进行。
试验方式应按具体阀种及标准规定执行。
3.压力试验的工业现状
3.1 一般工业现场的问题
压力试验的试验压力及实际保压时间是一个必须严格执行的参数,由于缺乏监督和一定的机构保证,操作过程中保压时间不足的现象严重,特别是在工作时间紧张的情况下。
而人工方法进行的试验结果归纳、整理,试验报告等文档材料的产生、保存、备查占据了相当大的工作量,有一定的差错率。特别是目前越来越强调的试压过程曲线的记录。
大多数阀门试验标准都规定:试验压力依据阀种、规格、试验项目与主体材料的最大许用工作压力呈一定的线性比例关系,而主体材料的最大许用工作压力的实际确定比较烦琐,目前一般阀门制造商,甚至一些专业检测机构只是将公称压力乘以相应的比例系数,或适当增加。加压和保压过程也是粗糙的目测和繁重的手工操作,存在一定的系统和人为误差。
3.2 专业机构的判定误区
这里所谓的专业机构是指专业检测和质量监督机构,在这类机构进行的压力试验,其数据应充分体现公正和合理,壳体试验时不应随意加大压力值,造成不必要的纠纷。
而密封试验和上密封试验时增加压力值反而带来不正确的判定。根据密封设计理论要求,合格密封的条件为:
其中:qMF——密封面上必需的比压;
[q]——密封面的许用比压;
q——计算的实际比压。
而 q=Qmz/Amf
式中:Qmz——密封副上的总作用力(包括介质压力);
Amf——密封副的有效作用面积。
可见,在很多情况下,增加介质压力,可以强化密封,不能达到合理检验的目的。
4.解决方案
4.1 试验压力确定的传统方法
其实,在我国阀门行业,一直有人在尝试解决试验压力与材料特性挂钩的问题,如把试验压力具体化,并标记于装配图上。将不同材料在常温下的最大许用工作压力值作为操作规范张贴于试压现场。
但这些方法没有能得到有效的推广,甚至尝试者也没能坚持下去,其原因一是试验现场环境较差,图纸资料难以保存;二是阀门产品种类繁多,特别是在目前已对全球供货的产业形势下,材料应用的范围非常广泛,各主要工业国的各种牌号的材料几乎都有可能涉及,很难在有限的空间罗列。
4.2 数字化方案
目前,压力试验过程中要解决的主要是三方面的问题,一是对压力信号的感应、设定以及对加压泵、压力调节阀等基本设备的控制,对于试验规范规定的试验参数、试验类别,能够从机构上予以保证;二是针对目前行业内普遍存在的,压力试验不与材料特性挂钩的现象提出现实解决方案,并使之在一般工业现场可行、可用。使压力试验过程更为准确和科学;三是对数据的整理工作,包括初始状态的设定,试验结果的判别,试验参数的归纳、整理、表达、保存、检索,以及辅助参数的管理等。
现代自动控制技术已进入以计算机技术为核心的数字式、智能化阶段,利用现代自控技术可以很方便地实现压力信号的感应、设定、反馈,对各种压力源的自动操作,对试验结果的自动分析、判别、处理,对试验过程的标准化、智能化控制以及各类数据的远程通讯。并且,结合数据库技术后使系统对数据处理的能力大为增强,可以轻松实现各类标准数据的快速检索、实时调用和有序组织。我们曾对现行压力试验台进行了数字化改造,取得了较好的应用效果。
4.3 应用研究
4.3.1 系统构成
系统由压力变送器、PLC(含必须的采集与处理模块)、触摸屏或触摸式平板电脑、压力控制与调节没备、电源及中间电路等组成(图1)。
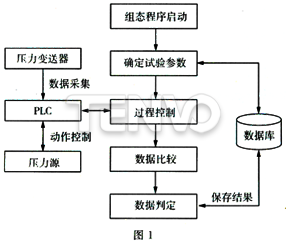
系统由组态程序启动,交互方式设定基础参数,PLC启动压力源并保证试验压力与保压时间,压力变送器采集的压力信号转变为电压值经PLC处理后送处理器分析比较,试验结束的条件为:试验压力已低于设定压力,或达到规定的保压时间。试验结束,系统自动整理试验报告与合格证(针对出厂试验),保留过程记录。程序设计中要设有稳压/补压模块,应对管路泄漏。界面设计时应考虑基础参数的交互干预,并能反写入数据库,满足特殊产品与非标元件的试压要求。数据库系统应具备多种数据检索方式,如:产品信息、日期、工号、工段号、合同信息等,提供质量管理的基本信息。
4.3.2 联机工作模式
对于多台位现场应采用联机工作模式(图2),联机工作时可以对各终端集中控制,数据资源也能得到共享与统一,减少不必要的元器件配置,便于检修和恢复。联机工作时,各终端之间、终端与上位机之间可采用以太网方式连接,固定IP地址,组态程序与PLC之间以OPC方式通讯,各控制单元遵守.Modbus协议。总线式PLC连接,分布式数据库结构,可提高反应速度和运行安全性,系统由上位机集中管理,但状态显示在上位机和终端之间可同时实现,便于差错监督和分步操作。
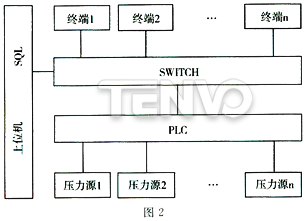
4.3.3 试压系统的改进
试压系统应加装手动/自动切换装置,便于系统检修和脱机工作,压力管路腰配有气压缓冲罐,减少对电子元器件的冲击。条件许可的情况下,应尽可能采取集成设计,减少过程误差和线路衰减,要有一定的警示和保护措施。在高、低压管路交汇处加装“两位三通”控制阀(原低压管路和高压管路切断阀可考虑取消),并在低压管路出口处加装止回阀,防止高压介质对低压系统的冲击(图3)。
5.结束语
压力试验是工业阀门生产和流通过程中的重要环节,数字化改造是解决其目前存在问题的理想手段,选择合适的控制方案、通讯模式、操作界面是实现这一过程的关键,而合理的技术指标、造价规模、一般工业现场的实用性研究十分重要。
天沃-硬密封蝶阀,与您资料共享!